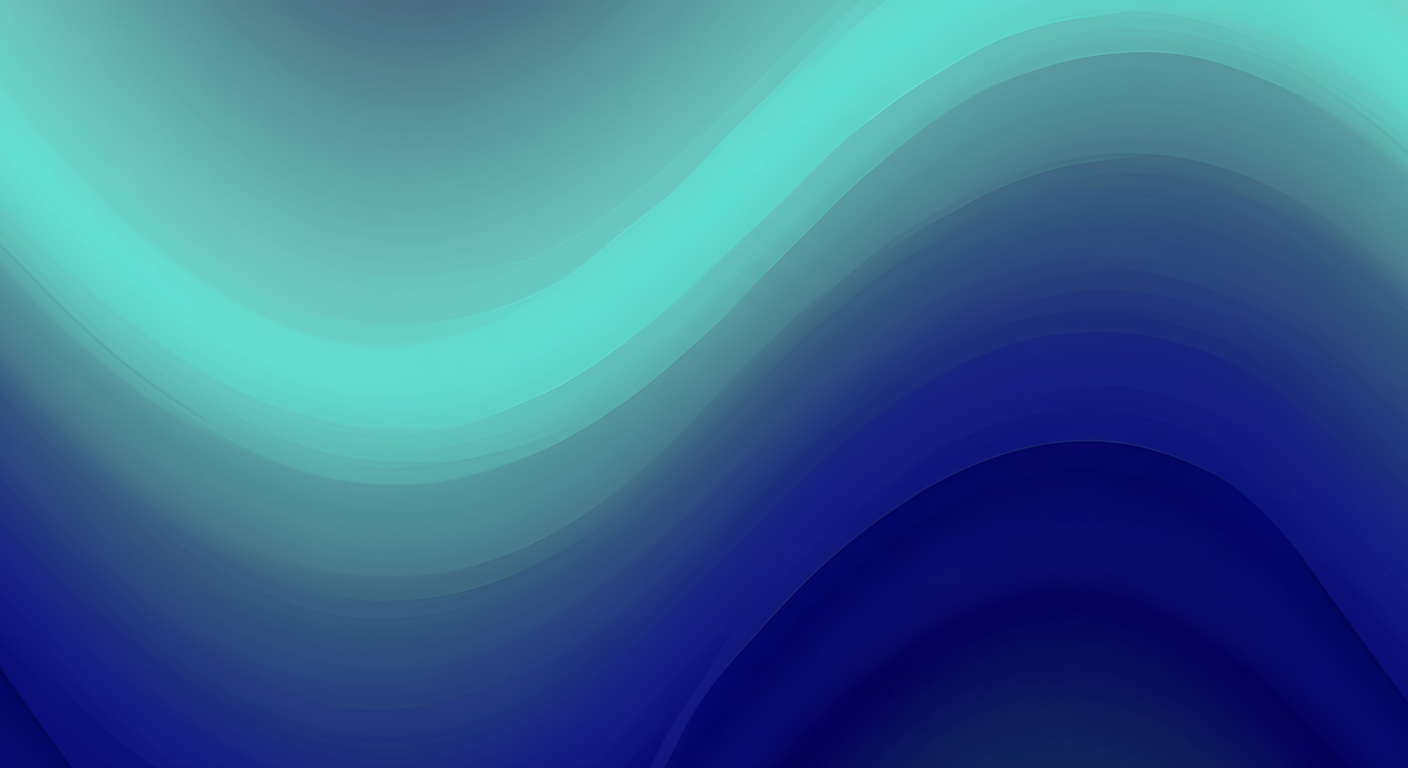
🔥📡 RF HTOL - Radio Frequency Hight Temperature Operating Life Test – In-Depth Technical Guide
The RF HTOL (Radio Frequency High Temperature Operating Life) test is an accelerated life test designed to evaluate the long-term reliability and durability of semiconductor devices operating with radiofrequency (RF) signals, while being exposed to:
High temperatures (typically 125 °C or higher),
Prolonged periods of electrical bias (power applied),
And most importantly: real RF functional activity, meaning the device is transmitting, receiving, or amplifying RF signals within its intended frequency and power range.
Unlike standard HTOL (which applies digital or DC stress), the RF HTOL test simulates real RF operation conditions, using:
Modulated or continuous wave (CW) RF signals,
Load matching circuits adapted to device impedance,
Filters, thermal control, and gain/power monitoring.
It's specifically applied to devices such as:
RF power amplifiers (RFPAs),
Local oscillators (LOs),
Mixers, RF transceivers (Wi-Fi, Bluetooth, etc.),
Frontend modules (FEMs),
SoCs with integrated RF subsystems.
How is the RF HTOL test performed?
RF HTOL involves a complex and rigorous process that includes:
1. Sample Selection
Samples are selected from representative lots across wafer positions and packages.
Ensures coverage of process and assembly variations.
2. Pre-Test Electrical Characterization
Measurement of all critical RF parameters such as:
Gain, P1dB, IP3, Noise Figure, VSWR, etc.
Devices must pass initial specifications before the stress test.
3. Board and Fixture Setup
Devices are mounted on custom burn-in boards specifically designed for RF testing.
RF signal integrity and proper matching are critical at this stage.
4. Stress Conditions
The DUT (Device Under Test) is subjected to:
Constant high temperature (typically 125 °C) inside a thermal chamber.
RF input signal (e.g., CW or modulated wave at 2.4 GHz).
Applied bias (voltage or current according to spec).
Load-matched RF output, often 50Ω or active loads.
Duration: From 168 hours up to 1000+ hours, depending on qualification needs.
5. Post-Test Characterization
All RF parameters are measured again and compared to initial values.
Degradations are analyzed in:
Gain,
Output power,
Noise performance,
Bias currents.
6. Failure Analysis (if needed)
SEM, FIB, X-ray, and de-encapsulation are used to identify root causes.
A typical LTOL test follows this structured procedure:
Sample selection:
Devices from a production lot are selected as test samples.
Initial verification:
Pre-test functional verification ensures all units are working before stress.
Mounting on boards or carriers:
Devices are mounted on special boards or trays that allow electrical bias during testing.
Test conditions:
Temperature: typically ranges between -40 °C to -65 °C.
Duration: often lasts 500 to 1000 hours or more.
Electrical biasing: Devices remain powered and active under nominal or stress-level operating conditions (e.g., full load, switching mode).
Monitoring:
Some systems allow real-time monitoring; in others, devices are periodically removed for interim checks.
Post-test evaluation:
After completion, devices undergo full electrical and functional tests to identify any failures or drift in parameters.
What types of failures does it detect?
The RF HTOL test targets failure mechanisms unique to high-frequency operation under thermal and electrical stress:
Electromigration in metal lines due to high current densities.
RF transistor degradation from accumulated thermal stress.
Impedance mismatch or damage to matching networks.
Dielectric breakdown from long-term voltage stress.
Frequency drift from altered internal capacitance or inductance.
Increased quiescent current (ICC).
Internal delamination or loss of adhesion in package structures.
Self-heating effects leading to unstable operation or power degradation.
Many of these failures do not appear under standard DC or digital HTOL, making RF HTOL essential for RF product validation.
Related standards
While general HTOL standards do not explicitly address RF operation, many can be adapted or extended to support RF HTOL scenarios:
JEDEC JESD22-A108 – General HTOL standard (can be adapted with RF functional bias).
JEDEC JESD47 – Reliability qualification standard (allows custom tests like RF HTOL).
AEC-Q100 Rev H – Grade 1/0 – Automotive IC qualification including RF subsystems.
IEEE 1521 – Characterization of RF devices and subsystems.
MIL-STD-883 Method 1005 – Defense-grade HTOL, adaptable to RF applications.
OEM Qualification Requirements – Apple, Tesla, Bosch, etc., often include specific RF HTOL requirements.
Conclusion
The RF HTOL test is an indispensable tool for validating the long-term reliability and functional robustness of RF semiconductor devices under real-world stress.
It delivers:
A realistic operational evaluation beyond digital stress.
In-depth insight into frequency-dependent degradation.
Confidence for deployment in critical wireless systems.
Compliance with industry standards and customer expectations.
In systems where communication is essential, the silence of an RF channel can be costlier than total power loss. That’s why RF HTOL isn’t optional—it’s mandatory.
What is it used for?
The RF HTOL test serves several critical purposes:
Predicting the failure rate of RF components under real-use conditions.
Detecting weaknesses in design, manufacturing, or packaging that only emerge under high-frequency operation.
Validating key RF performance metrics such as gain, output power, linearity, noise, and efficiency under extended stress.
Meeting reliability standards and customer qualification requirements, especially in critical industries.
Complementing digital HTOL, as RF devices present unique failure mechanisms not revealed through standard testing.
Why is it necessary?
RF HTOL is critical due to several reasons:
Different Operating Behavior:
RF devices behave very differently from digital ones.
Their failure mechanisms depend on frequency, signal power, and impedance.
Realistic Validation:
Digital HTOL cannot detect degradations that arise only under RF conditions.
Critical Application Environments:
Automotive, aerospace, defense, and medical industries rely on highly reliable RF communication.
A failure in RF circuitry may compromise entire systems or safety protocols.
Reduced Field Failure Rates (DPPM):
RF HTOL ensures robust performance over time, reducing returns and customer complaints.
Design and Process Feedback:
Early detection of RF-specific issues helps improve design and manufacturing quality.
Who uses it?
This test is used by companies and institutions involved in designing, manufacturing, or qualifying RF semiconductor devices, such as:
RF IDMs: Qualcomm, Broadcom, Skyworks, NXP, Infineon.
SoC manufacturers with RF modules (Wi-Fi, BLE, LTE, etc.).
Automotive electronics manufacturers (smart keys, tire sensors, etc.).
Aerospace and military system providers.
Internal QA and reliability engineering teams.
OSATs (Outsourced Semiconductor Assembly and Test) with RF capabilities.
Practical example
Case: Qualification of a 2.4 GHz Wi-Fi RF Power Amplifier.
Objective: Validate long-term performance and reliability of the integrated PA (Power Amplifier) in a Wi-Fi SoC.
Test Conditions:
Temperature: 125 °C
Duration: 504 hours
RF Input: CW at 2.4 GHz
Output Power: +20 dBm
Matched load (50Ω), monitored bias current
Results:
1 of 120 samples showed a gain drop >1.5 dB.
3 samples showed an abnormal increase in quiescent current.
Failure Analysis:
SEM and FIB analysis revealed electromigration in the output transistor’s base.
Corrective Action:
Layout improved for better current distribution.
Thermal performance of the package enhanced.