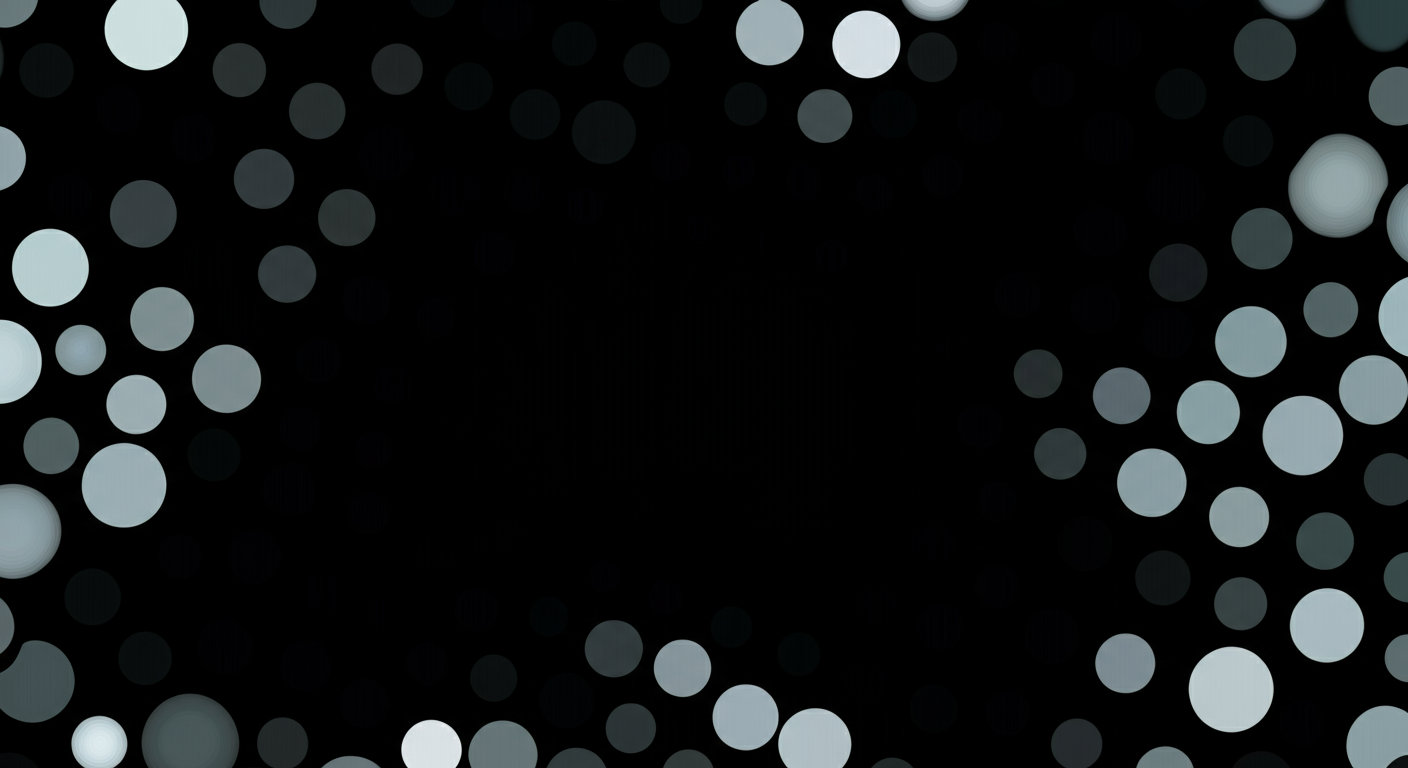
💧🌡️THBT - Temperature Humidity Bias Test
The Temperature Humidity Bias (THB) test is an accelerated reliability test designed to evaluate the resistance of electronic devices under extreme humidity, temperature, and electrical stress conditions.
During this test, Devices Under Test (DUTs) are simultaneously exposed to:
High temperatures (commonly 85 °C or up to 125 °C),
High relative humidity (typically 85% RH),
Continuous electrical bias (applied voltage across selected pins or areas).
The purpose is to simulate harsh environmental conditions that could be encountered during storage, transport, or operation in tropical, industrial, or outdoor settings. The THB test is also known as a moisture resistance and electrochemical stress validation test.
How is the THBT test performed?
The THB test is performed in a controlled environment and follows this general procedure:
1. Device Selection
Representative sample devices (by lot, package type, and technology) are chosen. DUTs are mounted on dedicated test boards or carriers for stress application.
2. Electrical Bias Application
A DC (or sometimes AC) voltage is applied across critical nodes (e.g., Vcc–GND, I/O pairs, substrate–lead frame).
Bias levels typically range from 80% to 100% of the device’s maximum rated voltage.
3. Environmental Exposure
The DUTs are placed in a climatic chamber with:
Temperature: typically 85 °C (can go up to 125 °C for harsher conditions),
Relative Humidity: 85% RH (hence the common name “85/85 test”),
Duration: 1000 hours (42 days) or more, depending on the test standard.
4. Interim Electrical Checks
Devices are electrically tested every 168 or 500 hours for parameters like:
Leakage current
Breakdown voltage
Switching delay
High-impedance behavior
5. Post-Test Failure Analysis
In case of failure, devices are decapsulated and inspected for:
Corrosion on bond wires or pins
Delamination or internal cracks (using acoustic microscopy or X-ray)
Dendritic growth or electromigration under SEM/FIB analysis
What types of failures does it detect?
The THB test mainly targets moisture- and stress-related failures, such as:
Electrochemical corrosion of metal traces, bond pads, or interconnects,
Ionic migration of metallic ions due to electric fields in humid environments (e.g., dendritic bridging),
Leakage currents between normally isolated terminals,
Reduction in insulation resistance,
Dielectric breakdown due to moisture accumulation and field stress,
Delamination between die, mold compound, or lead frame,
Cracking due to hydrolysis, internal swelling, or thermal cycling.
Related standards
While PTC is not universally defined by a single document, it is often conducted in compliance with established industry reliability standards:
JEDEC JESD22-A105 – Power and Temperature Cycling
AEC-Q101 / AEC-Q100 – Automotive Qualification Guidelines (includes power cycling and thermal stress tests)
MIL-STD-750 – Methods for testing discrete semiconductor devices (some PTC-like procedures)
IEC 60749-34 – Semiconductor devices — Mechanical and climatic test methods
JEITA EIAJ ED-4701/100 – Japanese equivalent for semiconductor reliability
Manufacturers may also develop internal specifications based on customer requirements or specific application environments.
Conclusion
The Temperature Humidity Bias (THB) test is one of the most essential tools in evaluating moisture robustness and long-term reliability of integrated circuits. It offers:
Early failure detection under realistic stress
Prevention of critical field issues
Qualification of packaging integrity
Valuable insights for material and process improvements
“Moisture is silent, invisible… yet deadly for microelectronics. THB testing makes it visible and conquerable.”
What is it used for?
The THB test is used to:
Detect latent or progressive defects caused by the combined effects of humidity, temperature, and voltage.
Evaluate the integrity of packaging materials and die-attach compounds against moisture penetration.
Test dielectric strength in the presence of conductive contaminants or absorbed water.
Reveal electrical degradation phenomena such as ionic leakage, corrosion, or short circuits.
Ensure product robustness compliance in critical industries such as automotive, aerospace, medical, and industrial electronics.
Validate packaging designs and process stability against delamination and moisture-induced stress.
Why is it necessary?
This test is critical for several reasons:
It simulates real-world environmental stressors found in humid, tropical, or outdoor conditions.
It helps identify aging and failure mechanisms not seen in initial testing.
Moisture is a leading cause of degradation in microelectronics and can penetrate many types of encapsulations.
Prevents warranty claims, field returns, and potential legal liabilities in mission-critical applications.
It is mandatory in industries such as automotive, aerospace, and medical electronics.
It provides feedback for materials selection, packaging design, and manufacturing process control.
Who uses it?
Semiconductor manufacturers producing microcontrollers, ASICs, MEMS, and power ICs.
Automotive suppliers for control modules, sensors, and ECUs subjected to outdoor or engine bay environments.
OSATs (Outsourced Semiconductor Assembly and Test) to qualify their mold and seal processes.
Medical electronics suppliers, especially for implantable or wearable devices.
Aerospace and defense sectors, where reliability under moisture is a non-negotiable requirement.
Telecom providers testing base station components and exposed infrastructure devices.
Practical example
Case Study: MEMS Sensor Reliability for Automotive Stability Control
Device Under Test: MEMS accelerometer with integrated ASIC
Application: Electronic Stability Program (ESP) in automotive
THB Conditions:
Temperature: 85 °C
Humidity: 85% RH
Bias: 3.3 V between Vcc and GND
Duration: 1000 hours
Interim Inspections: Every 168 hours
Test Results:
2 devices showed increased leakage current between power pins.
Delamination detected in one unit via acoustic microscopy.
Evidence of corrosion found on bond wires post-decapsulation.
Corrective Actions:
Switch to a more moisture-resistant mold compound.
Improve cure cycle for mold process to eliminate internal voids.